Empowering Quality in Construction: Insights from the CQA × Visibuild Webinar
- Jul 1
- 3 min read
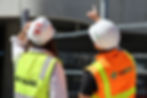
In our latest CQA webinar, we sat down with Damien Quinn, CEO and co-founder of Visibuild, to unpack the challenges — and opportunities — surrounding quality assurance on construction projects.
Hosted by Jerome Harris, General Manager - Quality at John Holland and CQA Chairman, the conversation didn’t just explore how digital tools are reshaping workflows — it went deeper, asking: Why hasn’t quality been given the same attention as safety, program, or cost? And what will it take to shift that?
Why hasn’t quality been given the same attention as safety, program, or cost? And what will it take to shift that?
“I Gave Myself RSI Doing Defects”
Before launching Visibuild, Damien spent over 15 years with Multiplex, delivering projects across Victoria and Queensland. His introduction to QA was brutally hands-on:
“I still have vivid memories of a strapped wrist from RSI. I’d done tens of thousands of defects on the Melbourne Convention Centre as a graduate — on a PalmPilot.”

It’s a story that hit home for many attendees — not just because of the outdated tools, but because it captured a broader truth: quality often falls to individuals, in isolation, at the very end of the process.
That early experience planted a seed. Years later, when one of Damien’s engineers — Shaun Phelan — left Multiplex to pursue a career in product management, the two reconnected to start something new. Their shared goal? Make quality assurance something that works for the people who actually use it.
What’s Gone Wrong?
Damien spoke openly about what many in the industry feel but rarely say aloud:
“Quality has historically been treated like a checklist to close out at the end — not something that shapes how the project is actually delivered.”
Rather than being integrated into program delivery, quality management is too often left to a single person, in a single folder, filed away for audit or handover — far removed from the people doing the work.
Digitisation Alone Isn’t the Answer
A recurring theme in the conversation was that digitising checklists does not guarantee improvement.
“Just going from paper to an app doesn’t solve the problem. You have to ask: who’s using it? When? Why?”
According to Damien, successful implementation requires two things:
Top-down leadership that gives project teams the green light — and expectation — to prioritise quality
Bottom-up adoption by trades, contractors, and supervisors — the people doing the work every day
That means building processes that are useful, not just auditable. If a checklist isn’t meaningful to the person filling it out, it simply won’t be used properly — regardless of whether it’s digital.
Quality Is Progress
One of Damien’s most powerful reframings came when he challenged how inspections are perceived:
“You can’t finish a pour, or install risers, or close up ceilings without an inspection. That’s not admin. That’s progress.”
In other words, inspections shouldn’t be an afterthought. They are the record of delivery. If the industry can start treating QA as a measure of progress — not paperwork — the benefits will follow: clearer communication, fewer defects, faster handover, and better outcomes for clients.
It’s a Win-Win — Especially for Subcontractors
Damien pointed out that subcontractors often stand to benefit the most — if given the right tools.
“Whether we like to admit it or not, a lot of subcontractors are running on tight margins but with higher risk. If they get QA right, they save time, avoid rework, and strengthen their position with builders.”
The message? Subcontractors can protect themselves with clear, timestamped records of completed work — resolving disputes faster and building trust with head contractors
Digital Construction and Cultural Change Starts with Inclusion
The final part of the conversation zoomed in on culture. Damien noted that many people currently being asked to use QA systems — subcontractors, site teams, suppliers — were never responsible for QA in the past.
“It used to be done for them, by someone else. Now we’re saying, ‘We need you in this process.’ That’s a big change.”
For that change to take root, it needs more than systems. It needs trust. It needs leadership that understands quality isn’t just about compliance — it’s about care, craftsmanship, and accountability at every level.
You can watch the full webinar HERE.